Oemeta‘s approach to fluid selection
In order to select a cutting fluid for any application, historically a “try-it-and-see” approach was taken, but this approach can be costly in time and resource, and often fails its objectives.
Uniquely in the industry, Oemeta uses industry-recognised fluid performance tests, normally used in R&D, to benchmark both your existing products and water quality prior to any product selection. This comprehensive data set can then be compared to the extensive range of products in the Oemeta portfolio, and improvement areas important to the customer can be targeted, resulting in a product being selected with a proven +95 % success rate in subsequent trials.
6 steps to success
- Samples of the current product and water are collected by an Oemeta technician - no disruption to production
- The samples are sent to the Oemeta HQ R&D laboratory
- Each sample is subjected to 50 industry-approved analysis methods
- Due to the rigorous testing required, results are available within 4–6 weeks (this timeline is much quicker if the product details have already been through Oemeta labs)
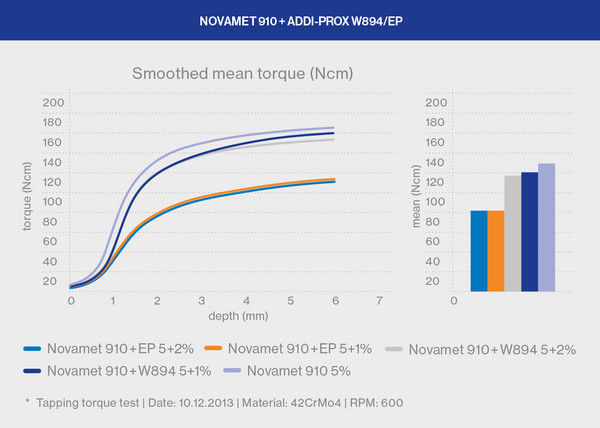
This includes:
- Foam generation analysis using your water quality
- Washing and wetting behaviour that affects both lubricity and machine cleanliness
- Lubricity
- Corrosion protection values
- Bio control
- Oil type and content used
- Identify substances that may affect operator health
- Compatibility with materials
The Oemeta representative will arrange an appropriate time to talk through the results:
- A complete overview of results, and what they mean
- Improvement objectives and current processes are discussed
- Product performance, in any given area, is down to ingredient type, quality and volume
- Oemeta review all data to identify a product that completely matches the discussed requirements
- This approach is unique to Oemeta due to the off-site assessment work, however Oemeta’s extensive experience with this trial method has proven its ability to deliver a clearer, and ultimately successful experience for all involved parties, with a +95 % trial success rate
Once performance gains are clear and viable for the fluid user, KPI’s can be set, and an Oemeta supported trial can begin. Here‘s how it works:
- Machines are cleaned by experienced Oemeta technicians at a time convenient to the trialling customer.
Normal machine turnaround times are 3–5 hours (depending on machine size and type) - Products are supplied on a sale-or-return basis with no cost to the trialling customer if KPI’s are not met
- An independent mixing station can be set up for the trial to make topping-up simple for the Operator
- Sample analysis plans and data capture is set up to monitor the KPIs
- Consumption is monitored via flow meters, fitted to the mixing station
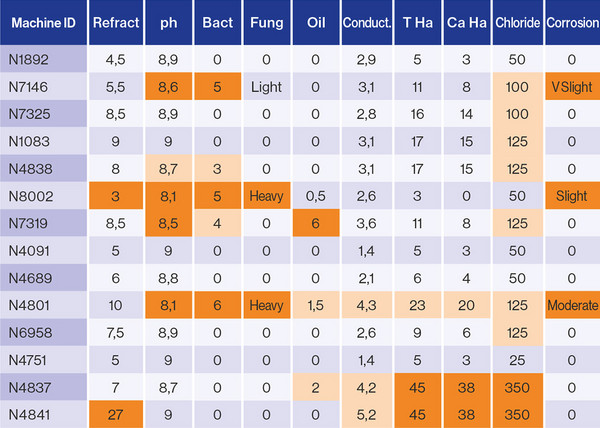
Upon completion of a successful trial, Oemeta coolants can be rolled out to machines systematically.
An example of how this is done:
- Sample all machines to establish coolant condition
- Transfer plan agreed with customer that takes into account using up remaining product, production restrictions, and only cleaning if required to reduce waste
- Compatibility with existing product will have been tested prior to trial to assess and confirm if ‘top-up over-the-top’ is an option to assist with a smooth transfer
- Set up robust mixing system to support transfer process
- Transfer period closely supported by Oemeta technicians using laboratory condition analysis and on-site testing
For the best results all-round, Oemeta collaborates with customers in a partnership by providing:
- Direct manufacturer supply and support
- A regular, experienced technician site-visit regime
- All products stocked in the UK, delivery within 4 working days of receipt, with next-day available
- UK and European laboratory support
- Free trials on fluid handling equipment if Oemeta technicians feel a significant benefit in process, and cost reduction can be achieved
- Monitoring and reporting options, both on and off-line, are available, that comply with audit requirements
- Bacteria testing in compliance with H&S requirements
- Direct support from Oemeta chemists, fluid, and mechanical application engineers
- On-site product handling training given
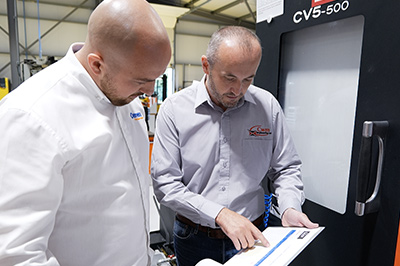
Why Oemeta?
Over the years our team has found a true passion for adding value to Oemeta’s impressive products through exemplary customer service, advice, equipment, and H&S and sustainability guidance. Manufacturing performance coolants since 1916, Oemeta always seeks ways to improve itself in line with evolving technologies, regulations, and customer requirements. Wherever machining coolants and oils are needed you can rely on the specialists, Oemeta, “The Coolant People”, to help.