About Gehring
Christoph Willi Gehring founded his company in 1922 and built his first honing machine in 1935. At that time, he probably wasn’t yet aware that this “finer and more precise surface machining of round bores” would one day make his company the world market leader for this machine technology.
Today, basic honing machines and systems are manufactured in Naumburg and put into system operation in Ostfildern near Stuttgart. A 24-metre-long plant is located in neighbouring Bad Cannstatt, for example, which processes V6 engine blocks with a cycle time of just 32 seconds. Steel, stainless steel, aluminium and cast iron are used to manufacture the high-precision components. The predominant processes are turning, milling, drilling and grinding.
Oemeta as a MWF partner
Without the honing machines produced by world market leader Gehring, the power density of today’s Formula 1 engines would be unthinkable. Gehring’s component plant in Naumburg had to work with even greater precision to ensure that the machines with the legendary dynamic tools met tolerance specifications. The aim of the initiative was to increase service life and reduce complexity while at the same time improving health and environmental compatibility.
In order to achieve these goals, the company opted to use Oemeta’s metalworking fluids (MWFs) for machining. The result: service life increased two and a half times and complexity was drastically reduced, while employees and the environment benefited, too. This was possible due to intelligent use of the innovative two-component HYCUT system.
Special grinding technology places the very highest demands on the metalworking fluid
“95 per cent of our machines go to the automotive industry,” says Gerhard Simon says the managing director of Gehring Naumburg GmbH & Co. KG., “and that includes the Formula 1 racing teams.” In order for these small 1.6-litre V6 engines with their high power density to produce the 800-1000 hp assumed at 15,000 rpm, the cylinders have to be honed perfectly to within half a µ.
Honing is not just crucial in Formula 1, however: this technology is now used in every combustion engine worldwide.
The special grinding technology used in honing with Gehring machines optimises combustion in the engine, reduces consumption, increases cleanliness and ultimately also complies with health guidelines. Obviously it is up to mechanical engineering to ensure this high level of performance is achieved. For this purpose, those responsible have been using Oemeta’s multifunctional two-component MWF HYCUT since 2014. The on-site trade and service partner is HMH Mineralöle.
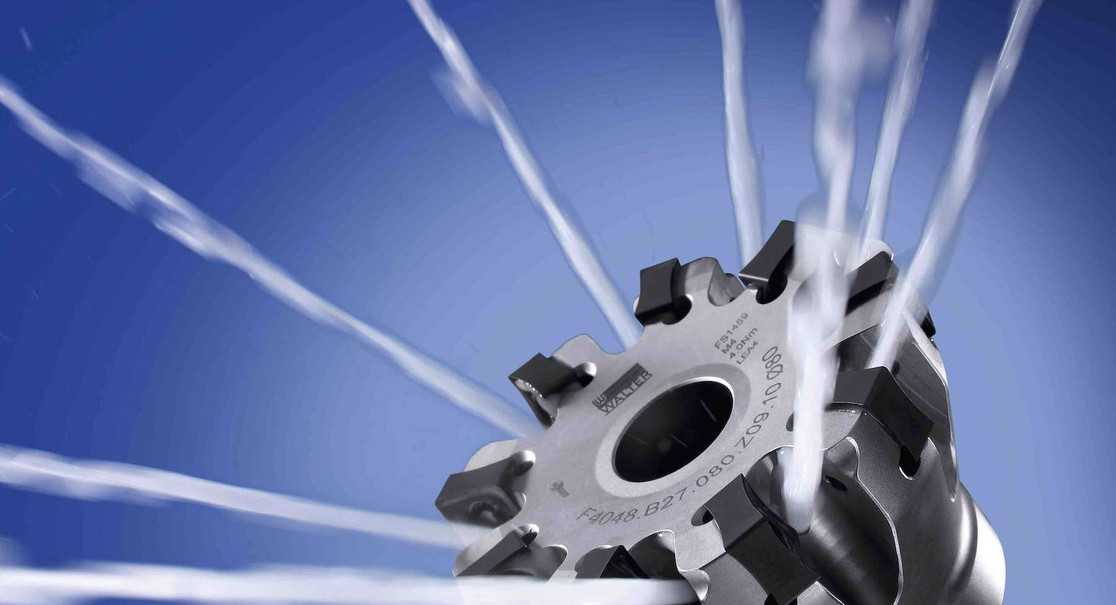
HYCUT
The core of the HYCUT system is ester-based oils. These offer the highest lubrication performance and reduce tool wear. They are also very stable over time. In addition, the excellent cleaning performance of the synthetic oils ensures clean machines and components as well as an exceptional good removal rate.
Reduction of the variety of coolants and advancements in manufacturing technology.
In addition to good surface quality – which was important to Gehring – it was also crucial to reduce the environmental impact and meet rigorous health requirements. Regular measurements, good on-site service and a quick response were to be standard. The aim was also to get away from rigid cycles which meant the individual containers on the machines had to be refilled every nine months. And last but not least, Gehring also wanted to reduce its high disposal costs.
Extremely hard water, tramp oil and foaming with the previous product.
These goals were quickly achieved by QMB Lutz Geweniger along with maintenance manager Ralf Köppl, the Oemeta sales team Torsten Schindler and Stephan Ebeling, and HMH area manager Peter Wachsmuth – all working in close collaboration. But there certainly were challenges, such as the very hard water in Naumburg with 35 °dH and a chloride content of 60 mg/l. What is more, there were a lot of coolant mixing stations where space was limited, as well as the issues of tramp oil and foaming with the predecessor product. The aim was also to reduce the variety of MWFs.
Wanted: the right metalworking fluid to meet all requirements in terms of technology, environment and health
Stephan Ebeling and Torsten Schindler are familiar with such requirements and are able to respond to them, though they’re also well aware “that the whole topic of MWFs is very complex in terms of technology, the environment and health management”. They instantly had a suitable multifunctional two-component MWFs in mind – Oemeta’s own HYCUT. At the core of the HYCUT system are ester-based oils that are compatible with each other when used as machining oils, MWFs or hydraulic media, so they save the need for intermediate cleaning, for example.
Adaptation to different process, material and lubrication performance requirements.
As a cutting and grinding oil, the water-miscible HYCUT offers extremely high lubrication performance, so it significantly reduces tool wear. Because it is made from synthetic ester oils, it is very stable to ageing. This ensures long running times. In addition, excellent cleaning performance ensures clean machines and components and an exceptional removal rate – especially in the case of grinding.
The special feature of HYCUT as an emulsion is the possibility of controlling the oil and the additive separately. This enables perfect adaptation to different performance requirements in terms of process, material and lubrication. The individual components can be added in specific doses throughout the entire service life of the emulsion. Once the right product had been found, the task was to implement a central supply system, taking into account the turning, drilling, milling and grinding processes and their requirements.
Four mixing stations for four production processes.
Two 1,000-litre tanks were installed at a central location, one for HYCUT ET 46 and one for the additive BX. Furthermore, piping was installed up to the coolant tanks, complete with hose reels and dispensing guns. Dosage is carried out by means of Dosatron mixing devices. Four stations are supplied by means of a hose reel and a dispensing gun and divided up according to the machining process.
Here, the concentration of the individual components is set to the required dosage according to the processing operations. In this way, every manufacturing process is supplied with the optimum mixture, whether as a machining oil or as a metalworking fluid.
For machining purposes, just 3-4 % HYCUT ET 46 and 3 % of the additive BX are sufficient; for grinding, 1-3 % HYCUT and 3 % BX. With the previous product, concentrations of over 10 % were required.
“One result was immediately noticeable,” says Geweniger: “The air quality in the hall improved very quickly, and employees felt more at ease.” Ebeling explains why: “The ester oil-based HYCUT forms fewer aerosols due to its droplet size.” Other improvements: the complexity of using such a large number of different oils was done away with, all machining processes produced better surfaces, the stock removal rate increased and the tools lasted longer. “Above all, however, the service life of the MWFs improved,” says Peter Wachsmuth of HMH, who initially carried out the control and maintenance on site. Based on regular measurements and logging of key details such as pH value, concentration and data, Gehring was able to refill coolant on a needs-only basis.
The following improvements were achieved:
- Improvement of interior air
- Reduction of the complexity caused by using numerous different oils
- Machining processes resulted in better surfaces
- Increased stock removal rate
- Tools lasted longer
- Improvement of the service life of the MWFs
Lutz Geweniger of Gehring is very satisfied: “Instead of having to stick to a rigid nine-month refill cycle, one filling can now do for up to around two and a half years. That was a really positive point for us.” After all, it means less frequent disposal – which is good for the environment and the controller, too. At the same time, HMH trained Gehring employees so that they are now able to take charge of maintenance and control. A QR code-supported software will soon make their work even easier.
As such, the final assessment is positive all round, with all goals having been achieved. “This is also thanks to our chemists and application engineers in Uetersen, where Oemeta’s headquarters are located,” says Stephan Ebeling: “They always manage to find the optimum solution to suit every on-site situation and every process.”