NOVAMET 910 and fluid management increase productivity while at the same time protecting the team and the environment.
About AUMA Riester
At AUMA Riester, 2,300 employees worldwide produce electric actuators for valves. Actuators are crucial components for every material flow, ensuring safety and the economic efficiency of entire industrial plants. Products made by this family-run business are to be found worldwide in power plants, water supply, offshore plants and refineries as well as in almost all areas of industrial production. The housings for turntables and control units are made of grey cast iron or cast aluminium and are manufactured at foundries worldwide.
In Müllheim, a wide range of components are produced using high-performance machining centres, including actuators, bevel gears and spur gear housings as well as output flanges and control unit housings made of aluminium. Machining steps include drilling, milling, turning, thread milling and thread forming. The machining centres in heavy and light machining generate large quantities of chips.
The challenge
In 2010 AUMA Riester decided to switch to modern metalworking fluids in its production – not only for manufacturing reasons but also due to considerations of health awareness and responsibility towards employees and the environment. The motivation here derived from values that have been firmly anchored in the family business for a long time.
The aim is to move away from metalworking fluids that contain questionable ingredients. While there had been no incidents or complaints from employees up to that point, nothing is yet known about long-term effects from frequent contact with the preservatives.
AUMA Riester also seeks to take responsible action before any possible dangers become known. Likewise, the aim is to stay one step ahead of the legal regulations: “We’re all aware that these are becoming increasingly rigorous in the context of growing health awareness,” says Andreas Völker, Group Manager of Resource Planning at Auma Riester in Müllheim.
In-depth analysis and recommendation of NOVAMET 910
AUMA Riester found Oemeta Chemische Werke GmbH to be a competent partner – not only a supplier but also a manufacturer of metalworking fluids with a proven track record. When the situation was analysed, residues of the metalworking fluid were found in the internal cooling of the spindles, for example. There was also an indication that the control of the boron-containing predecessor product was not ideally adjusted, thereby promoting fungal growth. The universal Oemeta metalworking fluid NOVAMET 910 was quickly agreed on as the right solution.
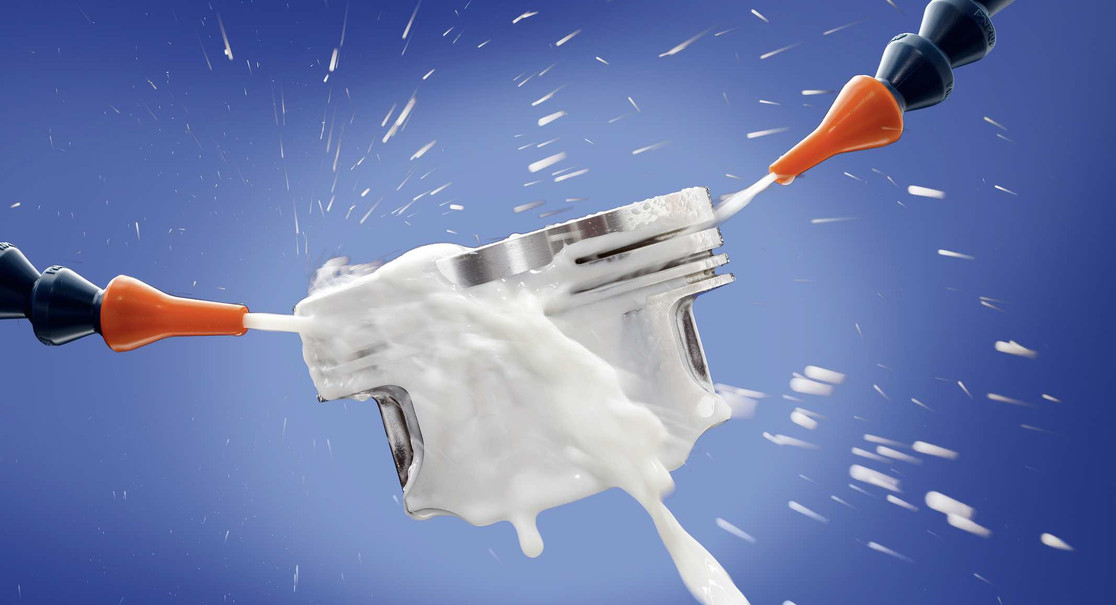
Solution:
„NOVAMET 910 is a broadly applicable product for machining in turning, drilling and milling. It offers a very high level of performance in a wide range of applications and materials as well as low consumption,” says Thomas Matter, Area Sales Manager at Oemeta and longstanding advisor to AUMA Riester.
High washing and flushing capacity as well as safe corrosion protection.
NOVAMET 910 is free of boric acid and formaldehyde, ideal for machining steel, grey cast iron, aluminium alloys and non-ferrous metals and ensures a high level of stability as well as a prolonged tool life. Recommended for use on individual machines and in central circulation systems, it ensures clean machines and workpieces thanks to its high washing and flushing capacity and reliable corrosion protection. It is also extremely skin-friendly. These were all requirements that that AUMA Riester was looking to meet.
Better tool life and cleaning effect.
A six-month test phase on two machines involving individual supply of 1,500 litres of MWF swiftly confirmed NOVAMET 910´s manufacturing properties and benefits as promised by Oemeta. “The tool life and cleaning effect in particular were far better,” recalls Andreas Völker. Drilling performance, especially with small diameters, also increased significantly due to better chip breaking. As a result, the change was made on all the machines.
“When we switched to boron-free and formaldehyde-free metalworking fluids for machining, the costs initially got out of control – contrary to our expectations,” recalls Andreas Völker. “When we commissioned Oemeta with fluid management, things suddenly improved and we now save around 40,000 euros per year,” says AUMA Riester’s Resource Planning Group Leader.
The metalworking fluid is usually changed after about six months based on the visual impression and if there is an odour. But since the purchase price of the boron-free and formaldehyde-free NOVAMET 910 is higher than that of the predecessor product, this puts more strain on production than planned. After operational interruptions in summer and at Christmas in particular, the metalworking fluid is fully replaced due to odour development. “In addition to product costs, there is also the machine downtime due to the fact that filling takes about 240 minutes – not exactly productivity-enhancing,” recalls Völker.
Fluid management extends the service life of the metalworking fluid
The AUMA managers found out that productivity loss is avoidable from Thomas Matter, who introduced them to fluid management – which Oemeta calls Coolant Management. The main point here is that the service life of the metalworking fluid is extended by about four times to two years, costs are reduced and the introduction of the new coolant is then closer to the original calculation.
For AUMA, Oemeta has compiled effective measures from a modular system to create a Coolant Management Package. In addition to the procurement of metalworking fluids, the service includes monitoring, maintenance, laboratory services, documentation management, control measures and disposal.
In this specific case, these are the services provided by Oemeta for AUMA:
- Weekly measurement of single-filled systems according to TRGS 611 and DGUV regulation 109-003, also electronically, with barcode system
- Complete documentation
- Preparation of a run-through protocol with comments on immediate measures
- Compilation of a weekly to-do list
- Provision of measuring equipment
- Preparation of care plan (after on-site assessment)
- Implementation of any immediate measures required, such as addition of concentrates, preservation in the case of bacterial infestation, addition of various adjusting agents
“What impressed us most in all of this was the professional approach,” says Völker. “Oemeta's service staff even have a walk-through route plan that optimises the pathways between the machines.” As a result of regular measurements and immediate action, the metalworking fluid can be used on each machine for a significantly longer period without any loss of performance. Lubrication performance is always optimum and “far superior to what it was before”.
The following improvements were achieved:
- Saving of metalworking fluid and increase of machine running times due to fewer new fillings
- Cost reduction in in the case of new filling, person hours and disposal
- Process reliability increased and CIP ensured.
- Avoidance of machine downtimes due to fungal infestation and extreme fluctuations in concentration.
What impressed Andreas Völker most, however, was the fact “that Oemeta offers this service and accepted the order even though it means they themselves sell less because we don't have to order new metalworking fluid as frequently.” In terms of Oemeta’s philosophy, this is by no means contradiction in terms, as Regional Sales Manager Gerrit Walker says: “We attach priority to people, the environment and long-term customer relationships – not simply making a quick profit.” This is why Walker always prefers customers who have the patience this requires. “Things improve quickly, but the ideal situation is when you have a period of months over which you can draw comparisons.”
The aim is for Coolant Management to become part of the continuous improvement process (CIP), contributing sustainably to increasing productivity. Everyone involved confirms that this has been impressively achieved at AUMA Riester – not least because AUMA Riester and Oemeta are family businesses and have similar values. And so beyond the considerable cost savings of 40,000 euros per year, that satisfying feeling remains of having contributed to employee health and the environment.