Successful partnership with Cwm Engineering
Since 2022, we have been supporting Cwm Engineering, a contract manufacturing company from Wales, with our metalworking fluids. Cwm Engineering has experienced impressive growth since its inception due to its continuous improvement approach and the high quality of its work. The company processes a variety of materials in both manual and CNC machines, including plastics, aluminium, steel and heat-resistant alloys. In addition to machine uptime and productivity, Cwm Engineering's focus is on the health, wellbeing, and safety of its employees.
The start of our collaboration
In 2022, Cwm Engineering was faced with the challenge of finding an optimum metalworking fluid solution for its diverse range of machines and materials. The increasing number and complexity of their machines made machine availability and productivity crucial factors for continued commercial success. Although the metalworking fluid used at the time was a branded product, it had a short service life and caused unpleasant odours and skin irritation among employees. After switching to another manufacturer, other problems arose. Although the new coolant had no nasty chemicals, its performance was inconsistent from machine to machine and there was a distinct lack of support by the new supplier. Cwm Engineering therefore turned to Oemeta.
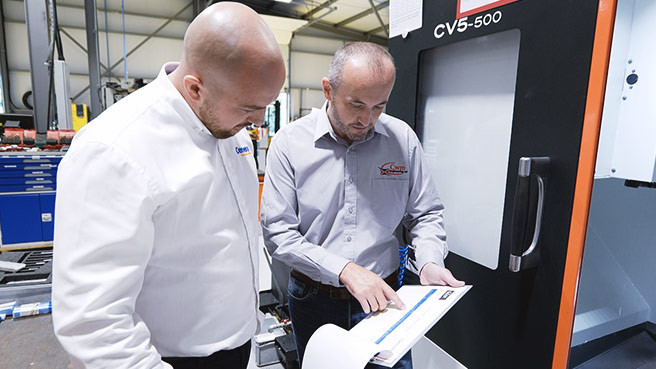
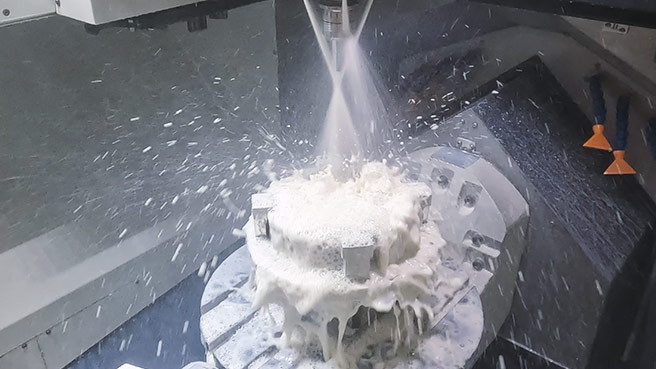
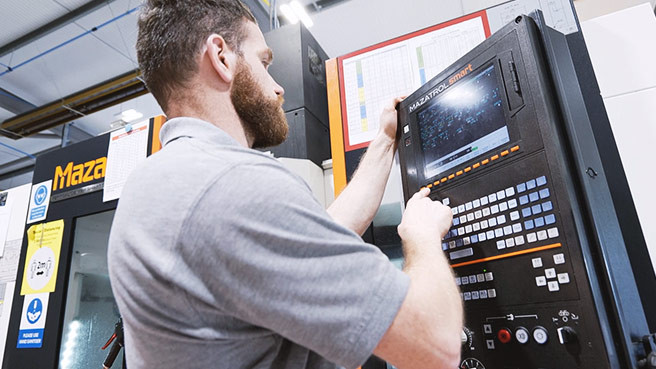
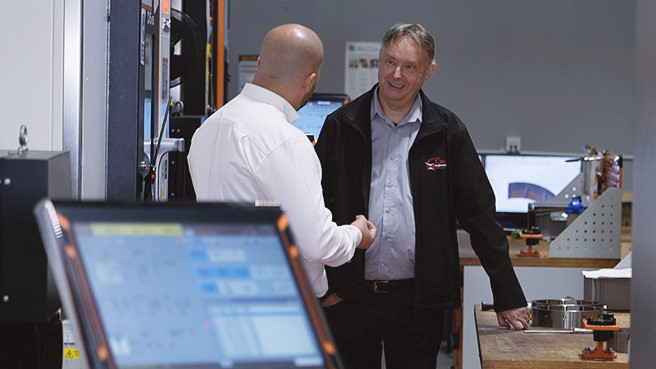
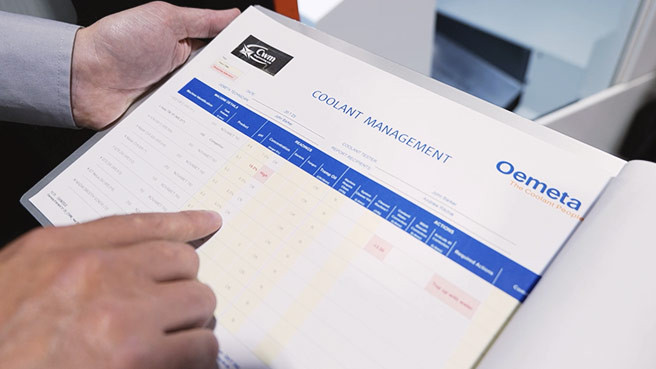
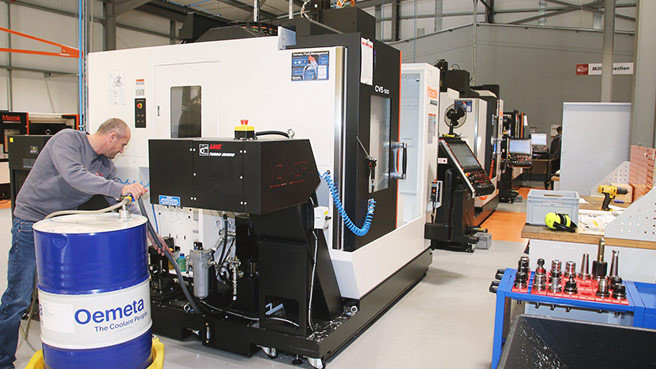
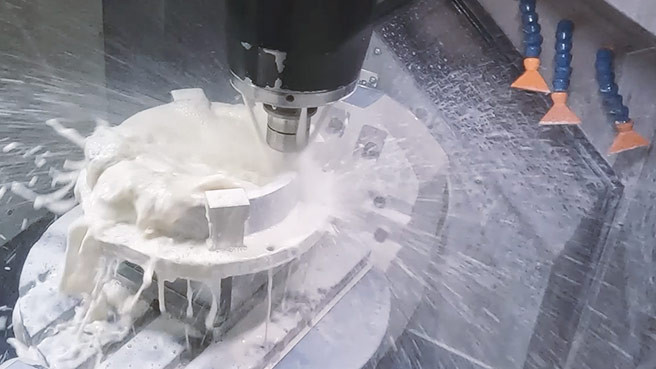







Our solution: NOVAMET 760
Oemeta took on the challenges and was able to successfully solve Cwm Engineering's problems at the time. After a detailed consultation, we recommended our NOVAMET 760, which proved to be the optimal choice for the contract manufacturing company. After a successful test in one of their machines, the Mazak VTC-530C, the life of the coolant increased by over 70%. With the clear results from the first machine, Cwm Engineering and Oemeta agreed on a phased approach to phase out the previous fluid and introduce the NOVAMET 760 in all machines.
Through our subsequent regular maintenance, we were able to achieve significant savings for Cwm Engineering on the cost of the coolant and its disposal. In addition, both the consumption of metalworking fluid and machine downtimes have been reduced.
NOVAMET 760 is designed for the machining of sensitive materials and impresses with its first-class material compatibility. With its impressive performance and efficiency in a wide range of applications as well as its low consumption, it is the ideal solution for demanding machining processes.
Our metalworking fluid in use on site
Watch the video to find out more about our collaboration with Cwm Engineering.
More facts and figures about replacing the metalworking fluid
The savings from the introduction of Oemeta's NOVAMET 760 were a gradual process over 12 months. By comparison, the previous metalworking fluid, at over £2600 per drum and consuming up to 6 drums, was costing the company over £15,000 per year. The Oemeta fluid, on the other hand, is almost 50% less than its predecessor, resulting in an immediate saving of around £7000. This would at least be the case if it was used at the same rate. With the remarkable improvement in fluid life, Cwm Engineering now only requires 2 to 3 drums per year - an excellent fluid life that will improve further once the rest of the previous supplier's fluid has evaporated from the machines.
What goes in, must come out. Cwm Engineering not only saves on coolant costs and the associated weekly testing and man hours, but also on fluid disposal. Cwm Engineering had to dispose of two 1000-litre IBCs of coolant two to three times a year. This equates to a cost of up to £2400. With an increase in fluid life of more than 70%, disposal costs will inevitably also decrease by 70% - it is estimated that Cwm Engineering can save an additional £1600 in disposal costs by replacing the coolant.
The cost reduction from implementing Oemeta's NOVAMET 760 has been overwhelming for the family business, but the benefits go much further. As Andrew Ritchie adds: "We have taps near each machine and we have a drum of NOVAMET 760 with a mixer on a trolley that can be wheeled to each machine. Once the drum and mixer are connected to the tap, we can easily top up the liquid in each of our machines. Simply doing this has saved us hours each week, and with Oemeta managing the condition of our fluid every two weeks, we save significantly on man hours spent on fluid testing. There is also no longer a need to shut down machines for sump cleaning, which can be a major inconvenience to our business."
Cwm Engineering Ltd
Cwm Engineering is a state of the art CNC precision engineering company based in South Wales. The family run business machines a wide range of materials including: Stainless Steels (all grades), Special Alloys, Titanium, Brass and Aluminum Alloys, Plastics (Delrin, Nylon and Peek), Castings and Extrusions.
More information about Cwm Engineering at: www.cwmengineering.co.uk